Beet Pulp Dryer
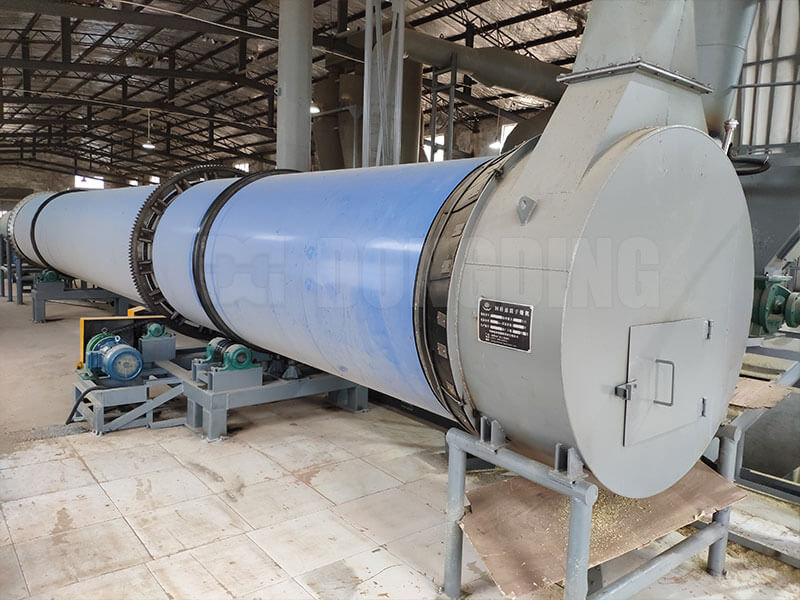
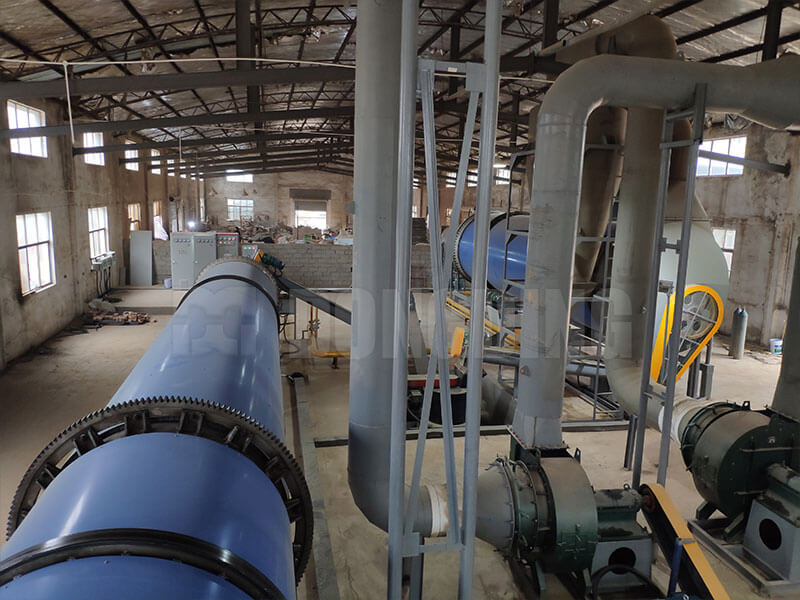
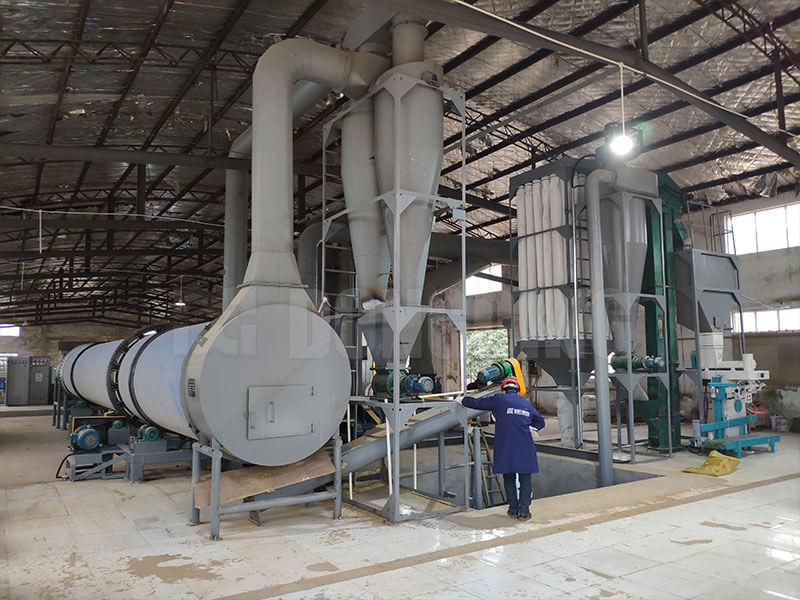
Beet Pulp Dryer
Capacity: 63.5-268t/d
Raw Material Moisture: 35~60%
Dry Material Moisture: 12~15%
Power: 78-135kw
Introduction
Beet pulp is the by-product of sugar extraction from sugar beets and can be used as an excellent animal feed ingredient. Drying beet pulp can effectively reduce transportation costs and enable further processing such as pelletizing.
The moisture content of beet pulp is about 75%-80%, which should first be dehydrated to 65% by a dehydrator to reduce the burden on the beet pulp dryer. The dehydrated beet pulp is then fed into the drying machine for processing. The entire dehydration and drying system can dry beet pulp with a moisture content of about 80% to 12%. At the same time, we can also equip subsequent pelletizing and packaging systems.
Advantages
1. Adopt intelligent control to automatically adjust operating parameters to ensure uniform and stable moisture content of dry materials.
2. Compared with a single-cylinder dryer, the floor space is reduced by about 40%, the civil construction investment is reduced by about 40%, and the equipment investment is reduced by 20%.
3. The internal structure of the dryer adopts multiple efficient lifting plate combination modes, which can effectively control the drying process and heat distribution. High heat utilization rate, exhaust gas emission temperature is lower than 50 ℃.
4. By using frequency conversion to control material flow, hot air supply, drum speed, the final moisture and output can be easily adjusted according to user needs.
5. Equipped with various new energy-saving hot air stoves, which are highly energy-saving, with controllable heating, easy operation, energy consumption reduced by about 30%, reducing operating costs.
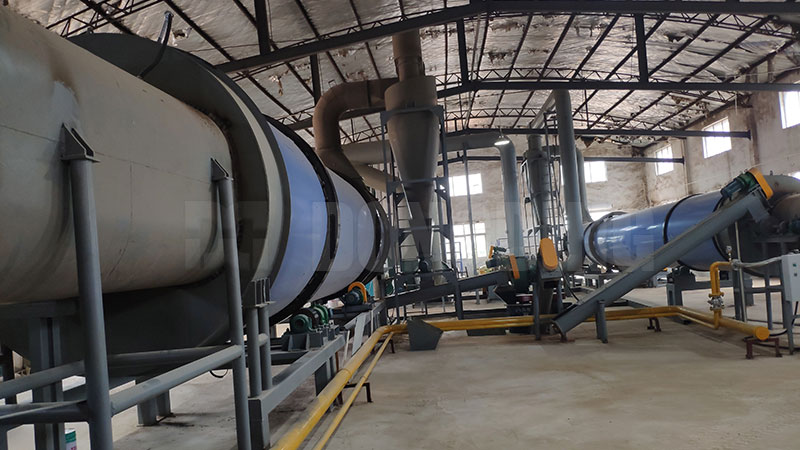
System
The beet pulp drying system is mainly composed of heat source device, feeding and discharging device, dryer host, dust removal equipment, induced draft fan, power distribution cabinet and other accessories. The dehydrated beet pulp enters the dryer drum through the conveyor and is fully contacted with the high-temperature hot air inside, thereby reducing the moisture. In addition, the dryer is equipped with a dispersion device inside, which increases the contact area between the material and high-temperature hot air and shortens the drying time of the material.
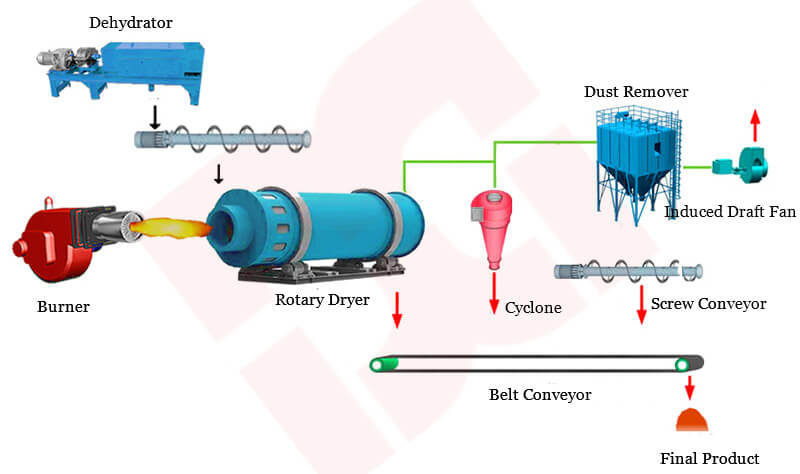
Technical Parameters
Model | DDSG2010 | DDSG 2210 | DDSG 2510 | DDSG 2512 | DDSG 2912 |
Capacity (T/D) | 63.5-144.5 | 67.5-154.0 | 83.5-193.0 | 100-227.0 | 120.0-268.0 |
Water Evaporation Capacity (T/H) | 1.850 | 1.976 | 2.427 | 2.912 | 3.432 |
Raw Material Moisture (%) | 35~60% | 35~60% | 35~60% | 35~60% | 35~60% |
Dry Material Moisture (%) | 12~15% | 12~15% | 12~15% | 12~15% | 12~15% |
Drying Temperature (℃) | 270℃±3 | 270℃±3 | 270℃±3 | 270℃±3 | 270℃±3 |
Power (kw) | 78 | 85 | 110 | 125 | 135 |
Weight (kg) | 25000 | 27000 | 35000 | 38000 | 43500 |
Area Occupancy (Width x Length) | 8m×18m | 10m×18m | 10m×18m | 10m×20m | 10m×22m |
Remarks: the moisture can be designed according to client’s requirement. |